Particle shape:
During the preparation of metal powder, the powder particles will show different shapes according to different preparation methods, such as spherical, nearly spherical, polygonal, porous sponge, dendritic and so on. The particle shape of the powder directly affects the fluidity and bulk density of the powder, which in turn affects the performance of the prepared metal parts.
Generally speaking, spherical or nearly spherical powder has good fluidity, it is not easy to block the powder supply system during the printing process, and can be spread into a thin layer, thereby improving the dimensional accuracy, surface quality of 3D printed parts, as well as the density and uniformity of the parts. Sex, is the preferred raw shape type for
3D printing. However, it should be noted that the particle packing density of spherical powder is small and the voids are large, which makes the compactness of the parts small and also affects the forming quality.
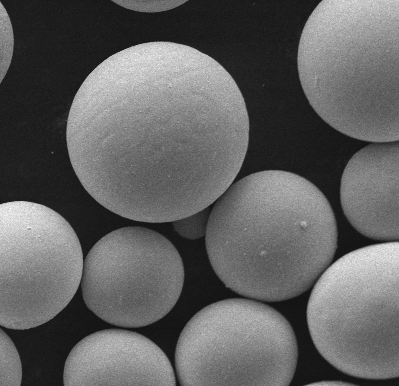
Powder particle size and distribution:
Generally speaking, the smaller the particle size of the metal powder, the more conducive to the smooth progress of sintering, because the smaller the particle size, the larger the specific surface area, and the greater the driving force for sintering. In addition, the voids between the fine powder particles are small, and the connection between adjacent powder layers is tight, which is beneficial to improve sintering densification and sintering strength. Small particles of metal powder can also be filled into the voids of large particles, which can increase the bulk density of the powder, thereby helping to improve the surface quality and strength of printed metal parts. However, it is not that the finer the particles, the better. If there are too many fine particles, the phenomenon of "spheroidization" will easily occur during the sintering process, which will easily cause uneven thickness of the powder. The so-called "spheroidization" phenomenon is a phenomenon in which the shape of the molten metal surface changes to a spherical surface under the action of surface tension in order to make the system composed of the molten metal surface and the surrounding medium surface have the minimum free energy. "Spheroidization" usually makes the metal powder unable to solidify after melting to form a continuous and smooth molten pool, so the formed parts are loose and porous, resulting in failure of molding.
The selection of metal powder particle size for 3D printing varies according to the heat source. Generally speaking, the particle size of powder formed by laser is 30-50 μm, and the particle size of powder formed by electron beam is 50-90 μm. High quality 3D printed metal products can only be obtained when the large and small particles of the metal powder are mixed in the correct ratio.